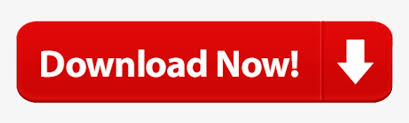
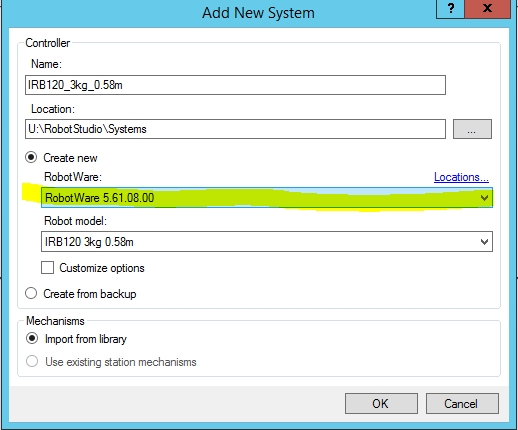
- ABB ROBOTSTUDIO PRG FILE INSTALL
- ABB ROBOTSTUDIO PRG FILE MANUAL
- ABB ROBOTSTUDIO PRG FILE SOFTWARE
- ABB ROBOTSTUDIO PRG FILE CODE
- ABB ROBOTSTUDIO PRG FILE PC
ABB ROBOTSTUDIO PRG FILE SOFTWARE
In this case, the dynamic development of software requires additional effort from the robotic systems integrators, among others in the form of organizing additional courses and trainings for their employees. A similar situation can be observed in companies responsible for launching new production lines. Factory managers strive to minimize production costs, and the increased complexity of robotic workstations makes employee training longer and more expensive. This is particularly relevant for older and middle-aged people, as they find it much harder to keep up with new technologies. The rapid acceleration of technological progress makes it difficult for process line operators to keep up with the exponentially increasing capabilities of the machines they operate. This is particularly important in the context of industrial robots, whose operating systems and programming languages provide great freedom in the development of advanced control software. The high level of automation and robotisation of modern production lines leads to a search for innovative methods of programming and machine control. Further research will focus on analyzing the influence of screen resolution and layout scale on the accuracy of trajectory generation. Thanks to the new method of robot programming, it is possible to quickly modify the path by the operator, without the knowledge of robot programming languages. The results confirmed the correctness of the application. Tests were carried out on the influence of the sampling frequency and the tool diameter on the quality of the reconstructed trajectory of the industrial robot. The application allows for changing the parameters of the robot and the parameters of the path drawing. The developed computer programmes have a modular structure, which makes it possible to easily adapt them to one’s needs. The obtained results were verified in online mode (on a real production station). Thanks to the development of a digital twin of the real robotic workstation, tests were carried out on the correct functioning of the application in offline mode (without using the real robot). The program for the graphic tablet and the operator interface was developed in C# language in Visual Studio environment, while the program controlling the industrial robot was developed in RAPID language in the RobotStudio environment. The paper presents elements of software development for offline and online control of a robot. Roslaunch abb_irb120_moveit_config moveit_planning_execution.The article presents the possibility of using a graphics tablet to control an industrial robot.
ABB ROBOTSTUDIO PRG FILE INSTALL
Sudo apt install ros-kinetic-industrial-core ros-kinetic-moveit Wstool merge abb_experimental/abb_experimental.rosinstall You can control the motion of the robotic arm on the rospc side.Īutomatic mode: "Motors On" and click the run button.
ABB ROBOTSTUDIO PRG FILE MANUAL
Manual mode: Program pointer "PP to Main", Enable makes "Motors On", click the run button.
ABB ROBOTSTUDIO PRG FILE PC
Roslaunch abb_irb120_moveit_config moveit_planning_execution.launch sim:=false robot_ip:= 192.168.1.100//( IP of robot PC )Ĥ. Confirm that ROSPC can ping ROBOTPC (set static ip, set virtual machine to bridge mode, ROBOTPC must be in the same network segment as ROSPC) Change the RAPID file: check the current winpc IP address and write it to the corresponding place in ROS_socket.sys.Ĭompile the abb and abb_experimental packages on the ROS side.Ģ. Run the ABB ROS server, so the robot will execute the motion commands sent from the ROS client nodeġ. ROS_motion.mod - issue motion commands to the robotĬompile the abb configuration package and call it with ROS.

ABB ROBOTSTUDIO PRG FILE CODE
Install the ROS server code on the ABB robot controller and configure the required controller settings.ĪBB ROS server code is written in RAPID language, using socket interface and multiple parallel tasks. In this case, there are usually two PCs, one running windows and ABB robotic arm, winpc the other running ubuntu and ROS, rospc. Set up the ABB RobotStudio simulator for ROS-Industrial driver.īy using a simulated manipulator instead of a real manipulator, communication simulation can be performed on ROS and ABB manipulators. Use a simulated robot in RobotStudio (you can skip this step if you use a real robot) Use ROS-I interface to install and operate ABB robotsġ.
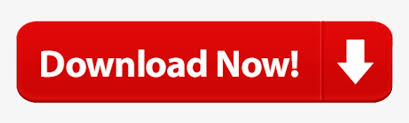